Chrisw8
Well-Known Member
- Posts
- 1,974
- Location
- Top of the Hill
Following on with being chuffed at painting my battery compartment .....
from this....
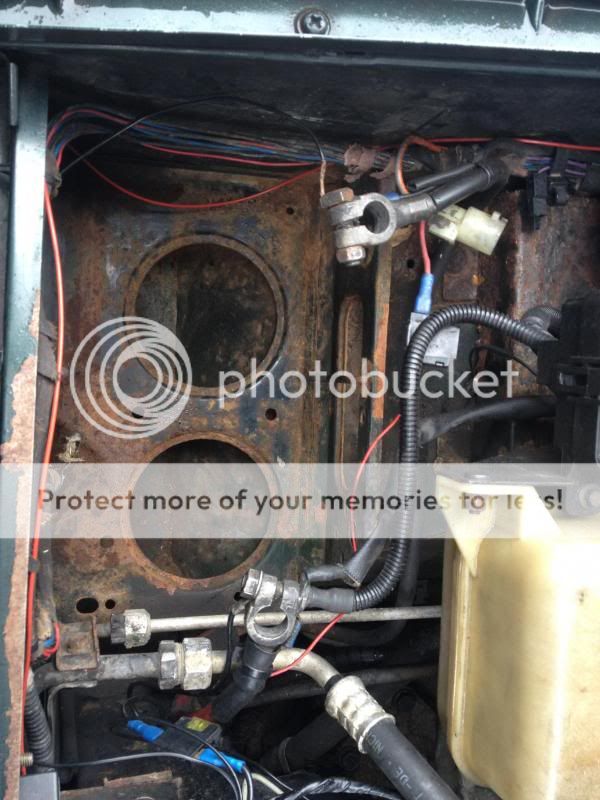
to this.....
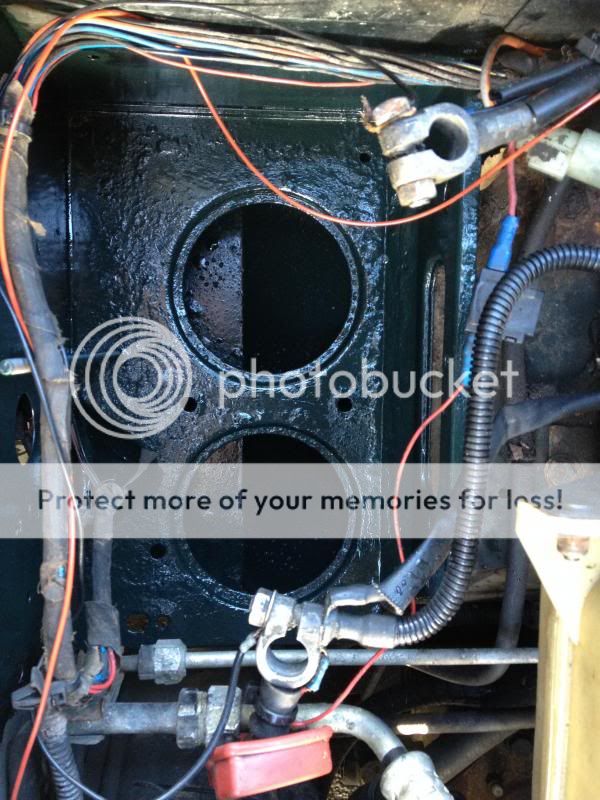
I thought I'd do a bit more and remove the fuse box / coolant tank holder....
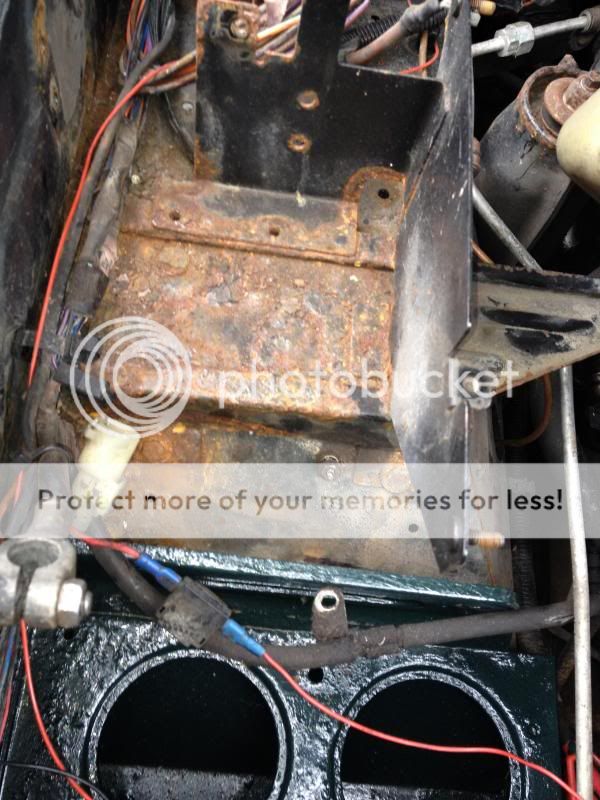
bad move
found lots of Rust in the Inner wing.... so I took off the Outer wing ( eventually)
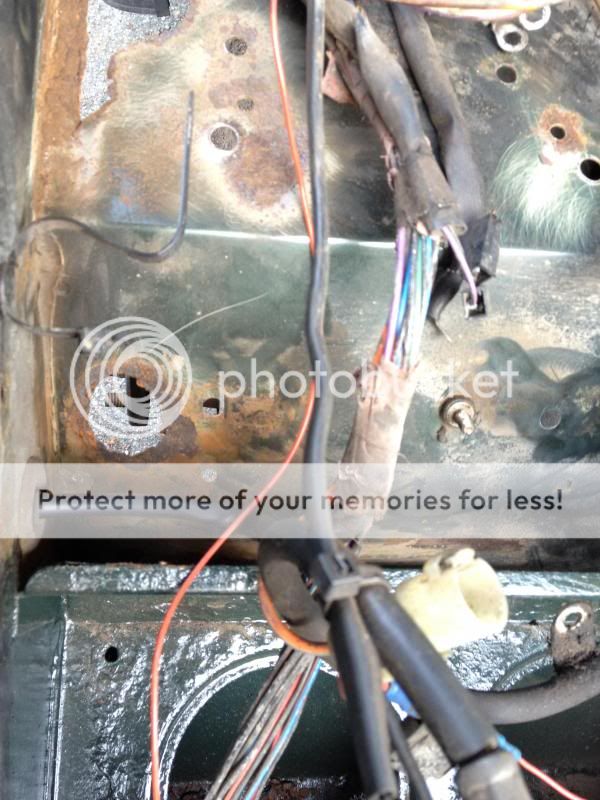
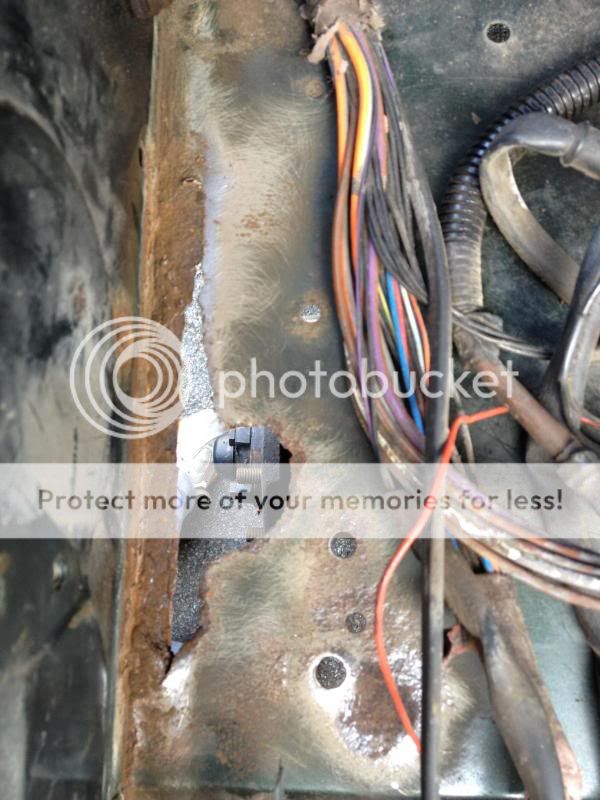
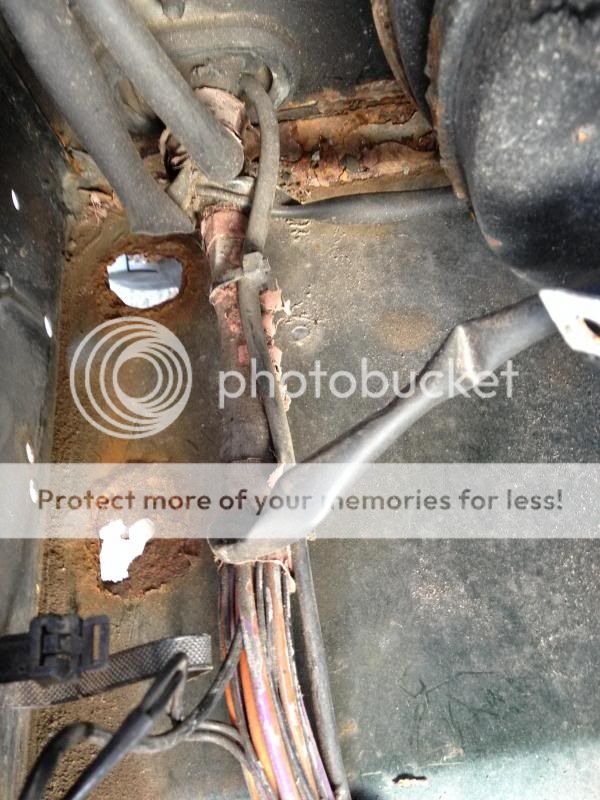
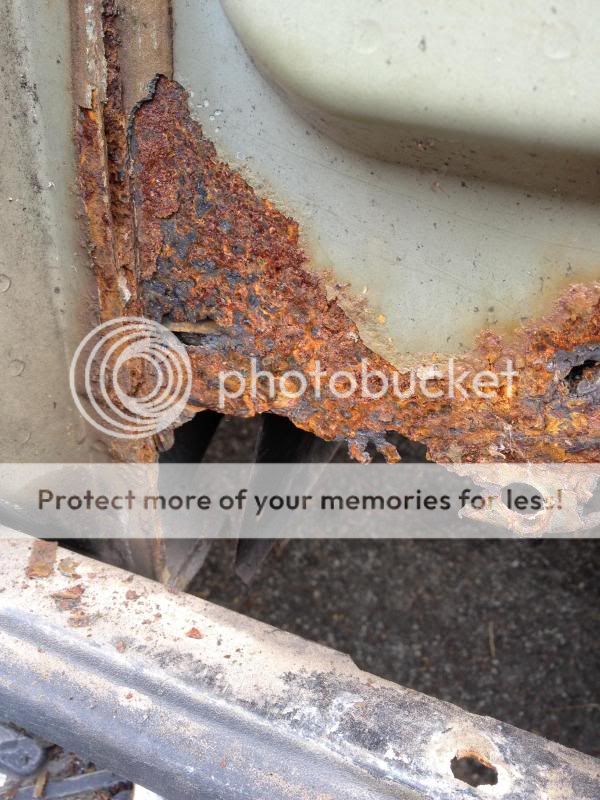
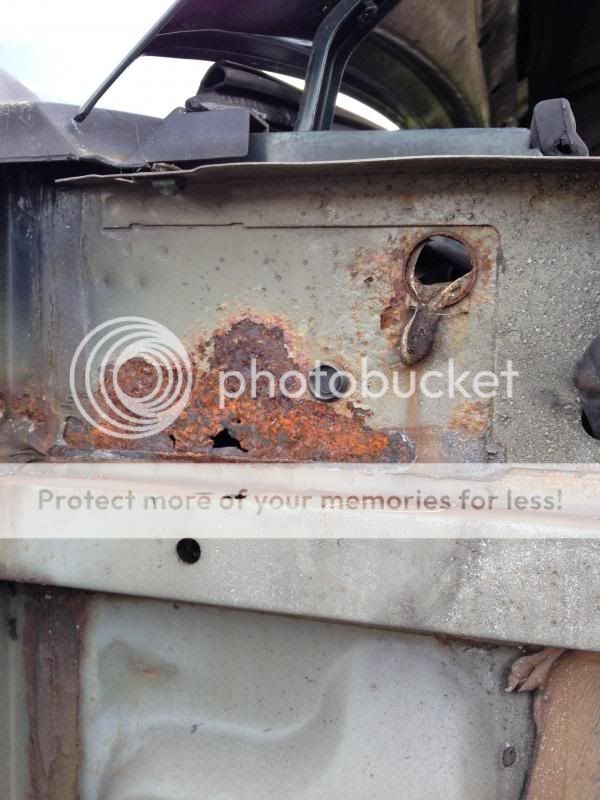
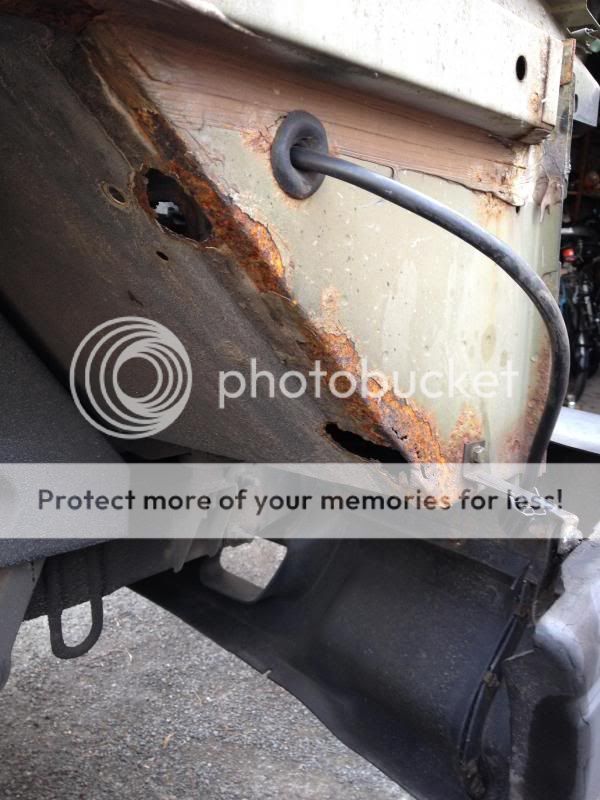
footwell too
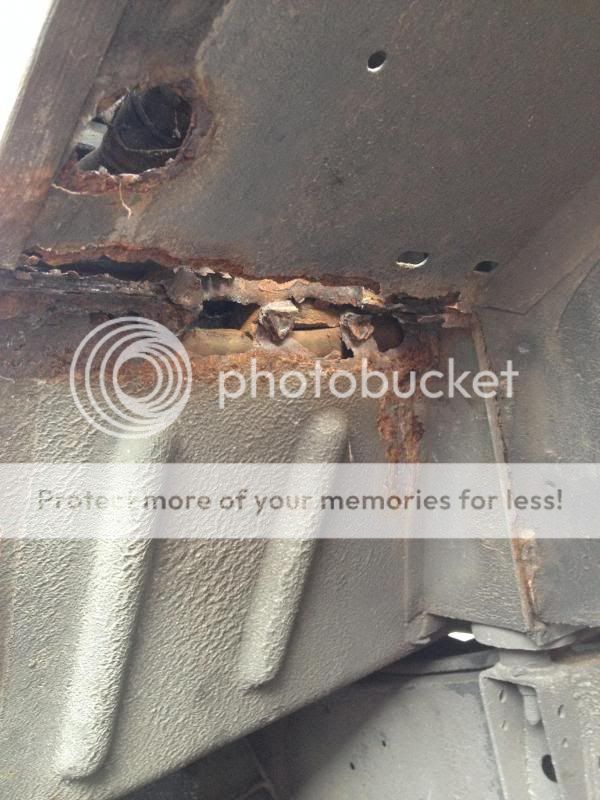
from above
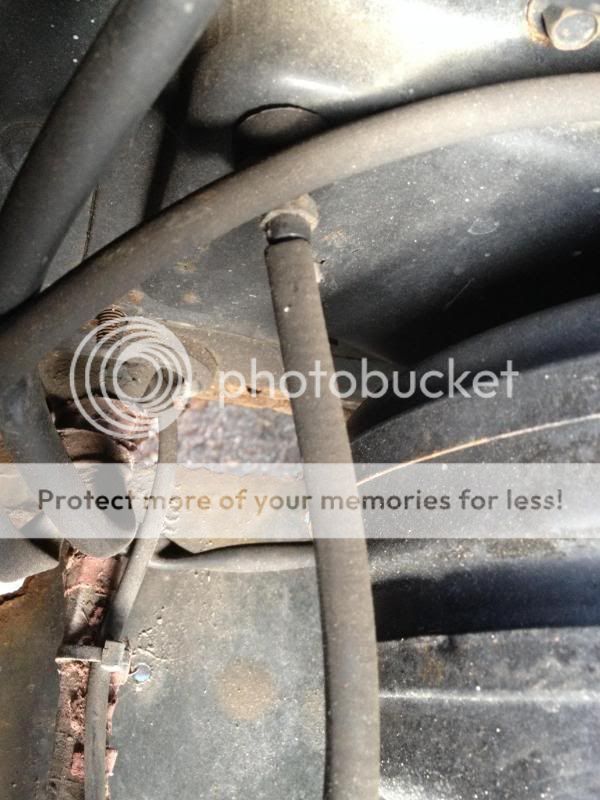
now, obviously a bit of welding needs to be done.
I shall leave the Numpty (how to)welding questions for now ...... but....
a ) should I get the necessary replacement parts from yrm , or should I try and cut out and weld plate in. ??? what would you do?
b)Most 'Important' Question, I if I was to get replacement parts ....... how do I get the old ones off ??
c) cant seem to find any parts for footwell , or that 'square' plate at top left.
that's all for now........feeling a bit depressed ...
oh, the n/s wing looks the same ....

from this....
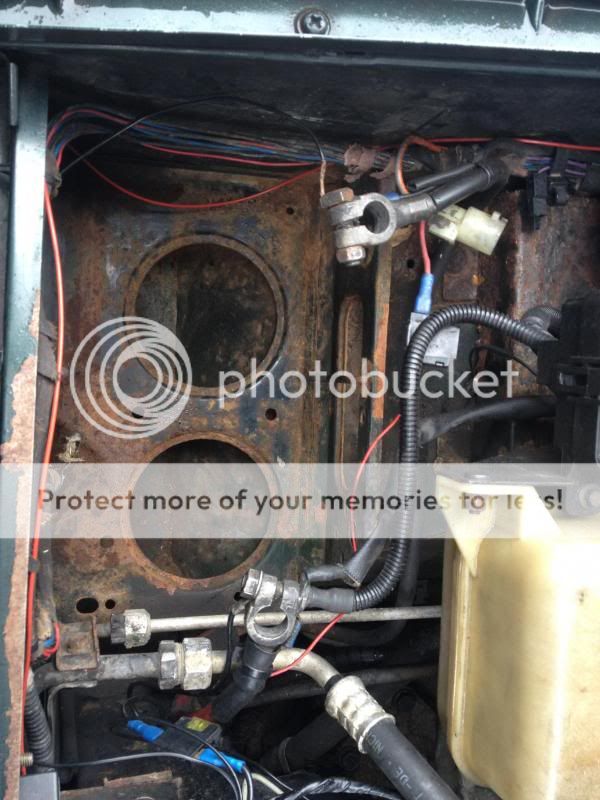
to this.....
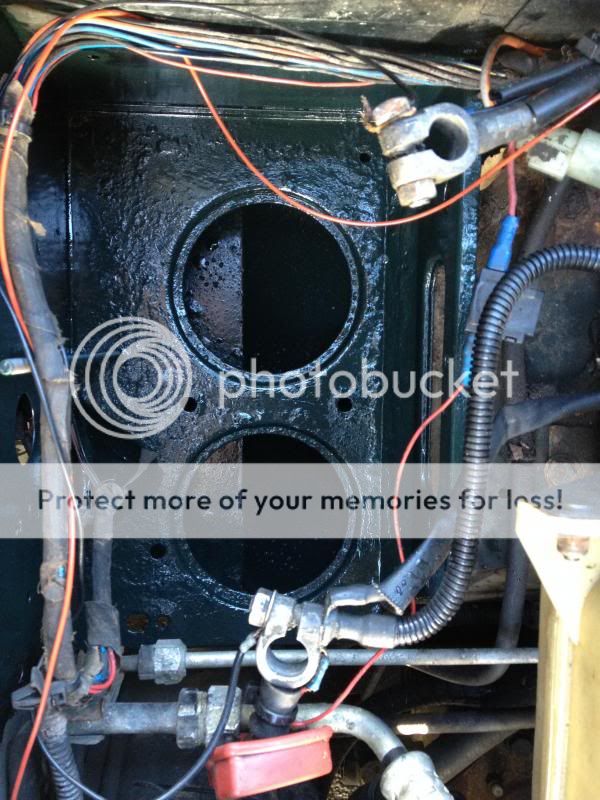
I thought I'd do a bit more and remove the fuse box / coolant tank holder....
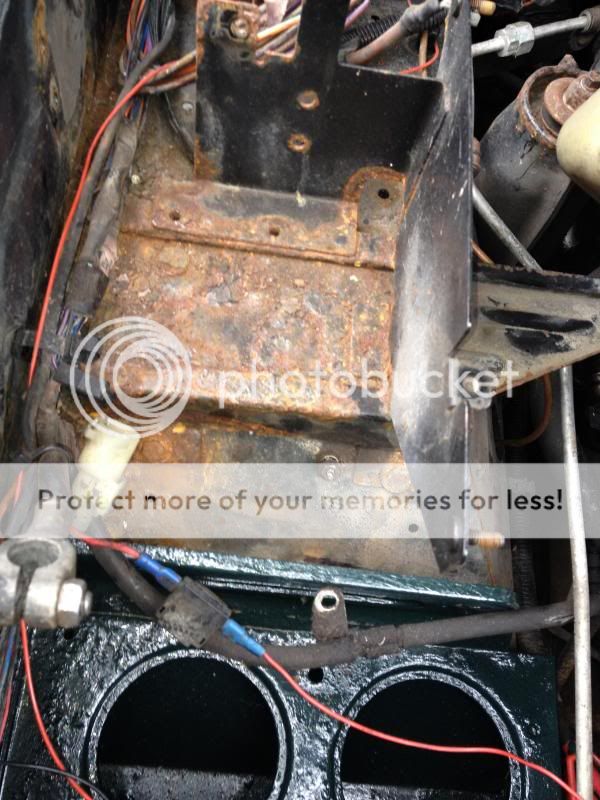
bad move
found lots of Rust in the Inner wing.... so I took off the Outer wing ( eventually)
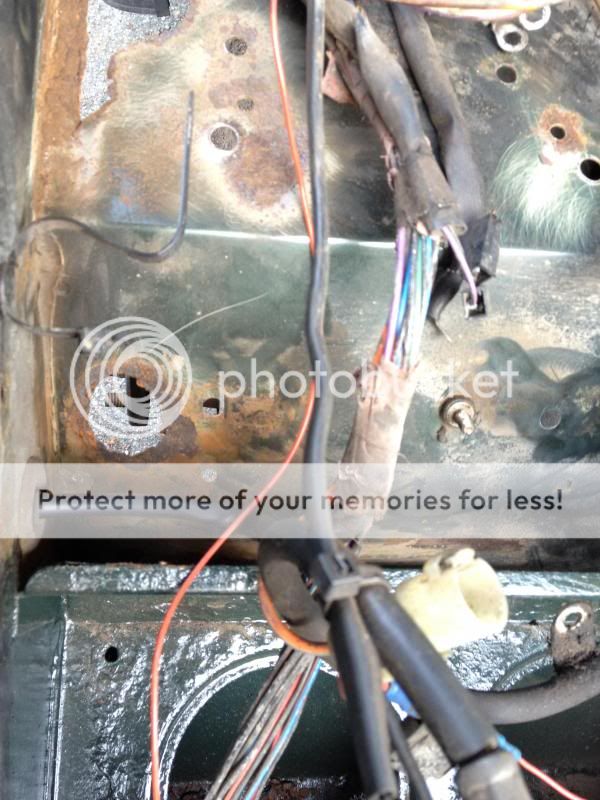
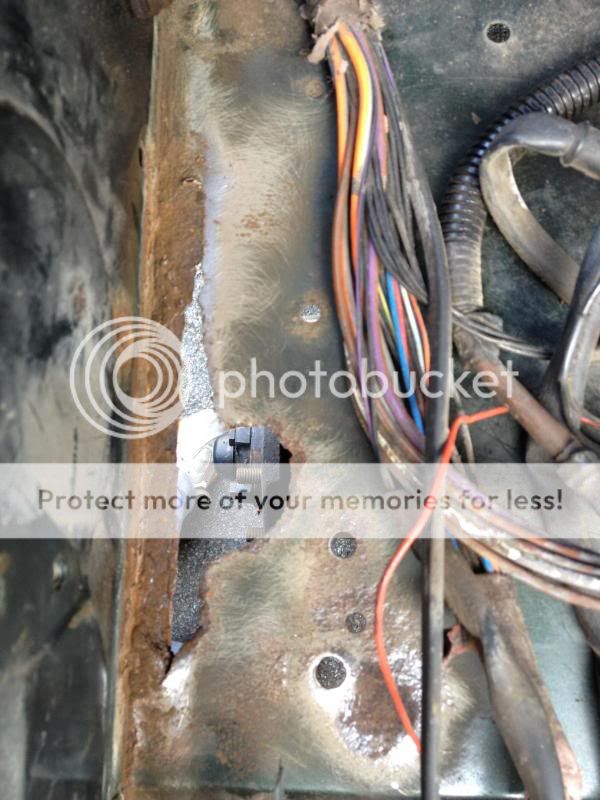
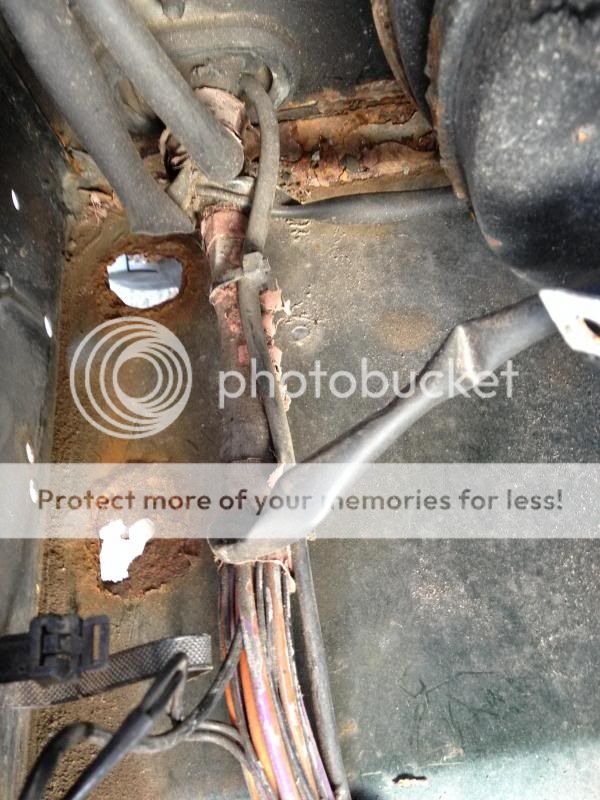
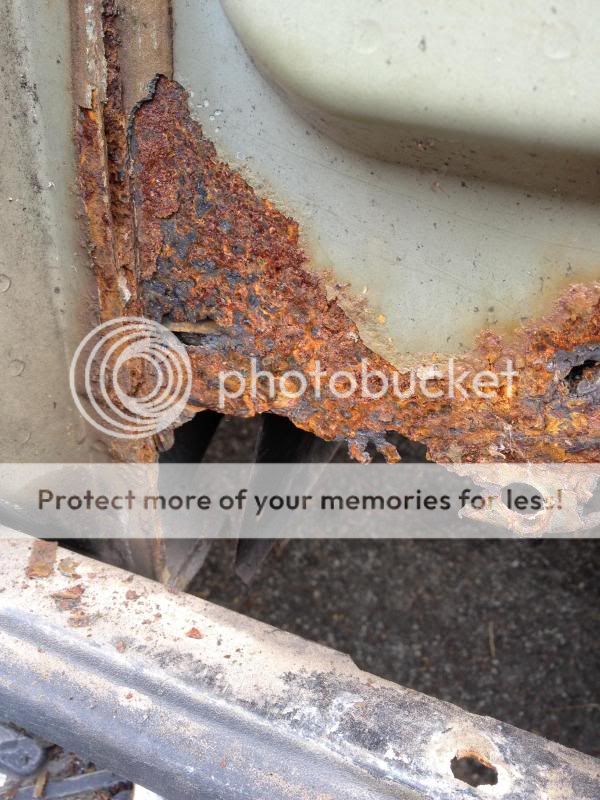
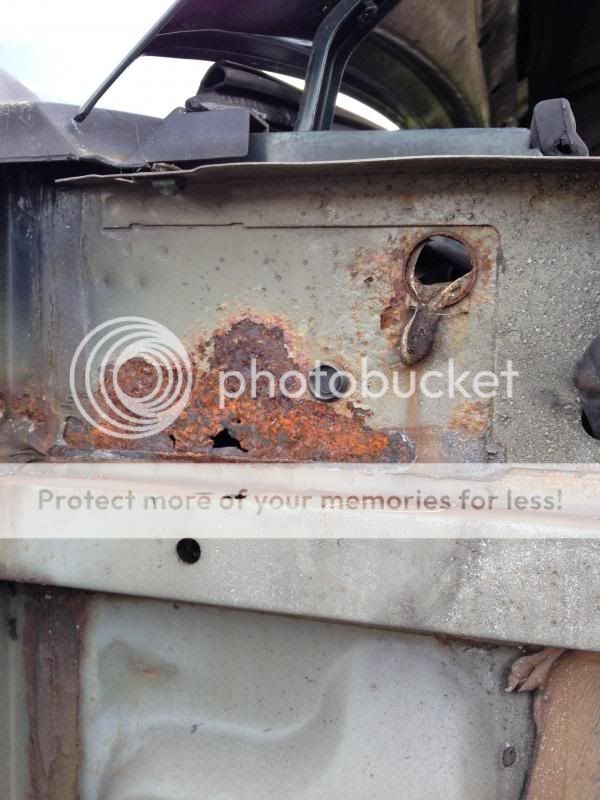
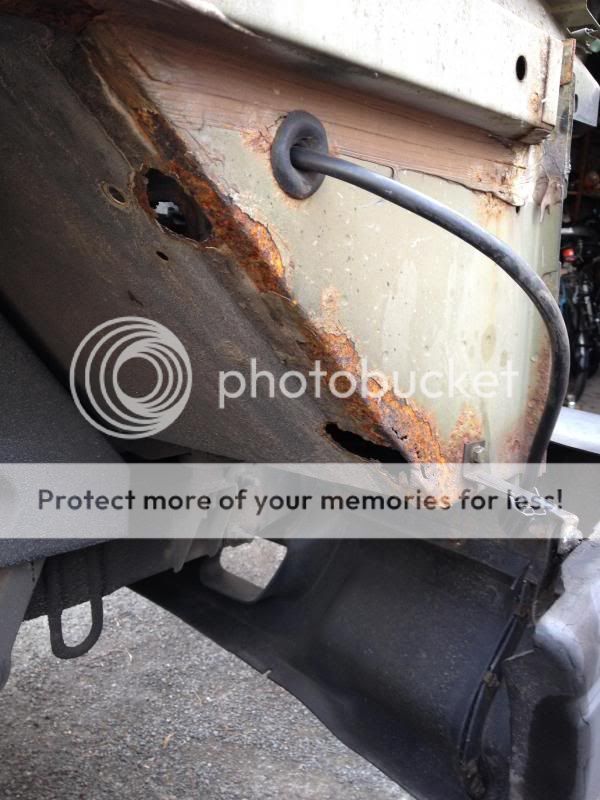
footwell too
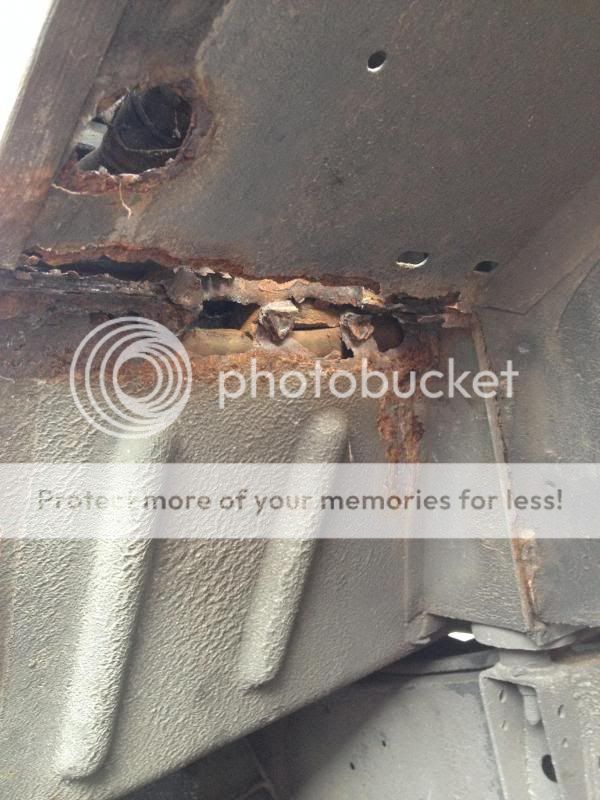
from above
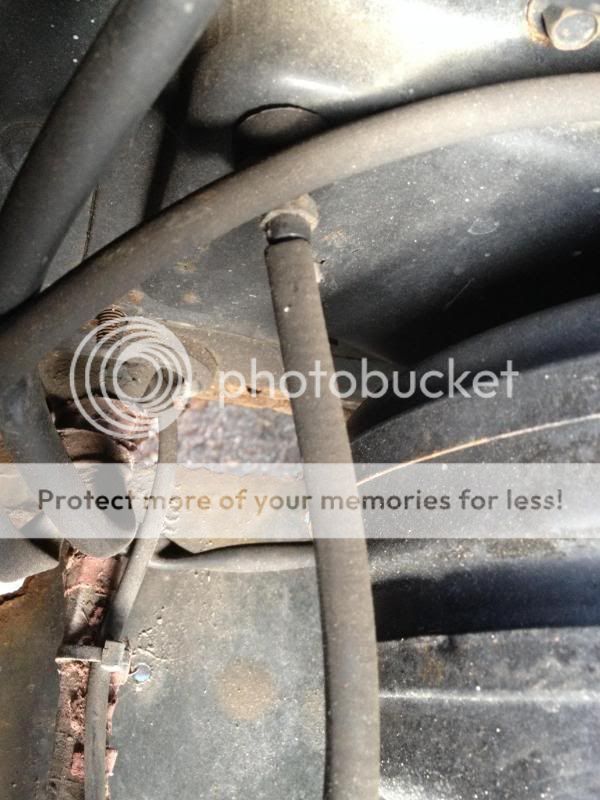
now, obviously a bit of welding needs to be done.
I shall leave the Numpty (how to)welding questions for now ...... but....
a ) should I get the necessary replacement parts from yrm , or should I try and cut out and weld plate in. ??? what would you do?
b)Most 'Important' Question, I if I was to get replacement parts ....... how do I get the old ones off ??
c) cant seem to find any parts for footwell , or that 'square' plate at top left.
that's all for now........feeling a bit depressed ...
oh, the n/s wing looks the same ....