bit more progress this weekend and then tonite a problem,
crank in and then the T seals to do, I got the btm edges in using a steel rule for a start and then used a thin edge either side to keep the bulging seal in while tapping from above moving each side a bit at a time, it didn't shave any off but stretched the seals you can see at the top.
Measurd the nip on the mains and con rods with one loose nut and all ok , pistons went in good using
the compressor tool, set gaps to avoid thrust sides and gudgeon pin area
replaced the two o rings on vacuum pump the inner shaft one was a pig, but hard and brittle and eventually it snapped and got it out with a cod hook,
oil pump end float ok, small amount of scoring on gears b
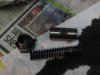
ut will replace the plunger and spring with genuine LR bits
cleaned oil filter h
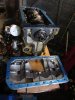
ousing
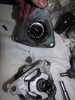
I replaced the rear core plug it was good condition but surprised now much rust is in the passageways , plan now to remove the 3 on the side to jet wash out, ladder frame on with some blue hylomar, sounds good stuff as you can pull it apart and stick it back on
oil pump on with a small amount of stud lock if youre lucky when you drop a bolt it may fall behind the side cover plate and you can get it with a piece of wire

ive put the sump on loose to keep dust out until oil pump bits come
next problem was how to get the dowty seal on that I fitted a year ago, I made a seal inserter out of an ice cream tub and cut the rounded ends off push thin end through seal and fat end on crank end went on a doddle.

flywheel on and turned engine round and had a go at timing
This is the problem
and im not quite sure where I went wrong I had flywheel locking pin in, and timing pin in pump, the crank key in line with arrow and the cam dot in line with marker
I believe I tensioned up but had the 3 bolts loose and things moved a bit , the pin got tight I pulled it out with pliers and removed belt
as you can see no way to get the pin ion now and turning the pulley wheel a bit does not sort it
ive got the other cogs back where they should go but how do I get this sorted to get the pin back in
@jamesmartin
thanks
apart form this hiccup next job is start stripping the head down now the workbench a bit cleaner