florncakes
Member
- Posts
- 35
- Location
- Bicester
I'm replacing the timing belt on my defender, due to a previous mechanic not tightening up the nose bolt adequately! The rear keyway for the timing is fine, no concerns. The front keyway which drives the ancilliaries is wide as the last keyway fell out in service and was rattling around. Question is, armed with new keys, what would you recommend to fix the gap?
I've no wish to replace the crank (although money no object I would do), no wish to weld/file/grind a new keyway.
I can make / have got some 1mm steel sheet at work, and some loctite and superglue here.
Some figures - the rear keyway is 6.3mm wide and the new key is a good fit.
The front keyway is 6.4-6.5mm wide at the bottom, 7.5mm wide at the top... err!
[GALLERY=]
[/GALLERY]
Your thoughts and experiences would be appreciated please.
I've no wish to replace the crank (although money no object I would do), no wish to weld/file/grind a new keyway.
I can make / have got some 1mm steel sheet at work, and some loctite and superglue here.
Some figures - the rear keyway is 6.3mm wide and the new key is a good fit.
The front keyway is 6.4-6.5mm wide at the bottom, 7.5mm wide at the top... err!
[GALLERY=]
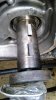
Your thoughts and experiences would be appreciated please.