series2steve
Active Member
- Posts
- 113
- Location
- deal ,kent
hiya lads im half way thru this and had some battles ,the latest being the clutch
rrc v8 onto 1967 2a non syncro series box
the rr flywheel has been drilled for 9"[i keep reading should be 9.5"]
this is the only 9" cover i can find [the existing] even then il have to enlarge all 6 holes to get last 2 bolts in
so does anyone have anything to say about using this cover? ,cheers boys ,steve
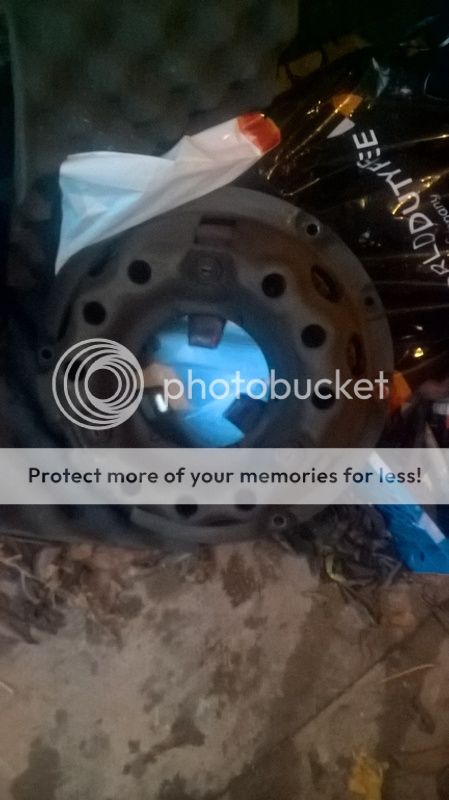
rrc v8 onto 1967 2a non syncro series box
the rr flywheel has been drilled for 9"[i keep reading should be 9.5"]
this is the only 9" cover i can find [the existing] even then il have to enlarge all 6 holes to get last 2 bolts in
so does anyone have anything to say about using this cover? ,cheers boys ,steve
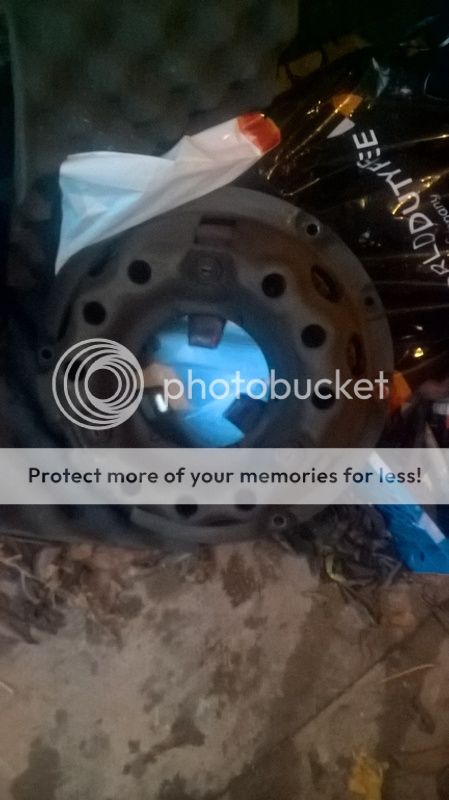