Zenerdiode
Member
- Posts
- 35
- Location
- UK
Having recently Posted a method of how to remove the carbon cemented copper-washers from the base of Injectors in their cylinder-head bores, which has been widely accepted as well as copied, I will now move forward to yet an additional benefit concerning the same copper washers. I hasten to add that what I Post is applicable to all.
Copper is not that much different to other metals. It is malleable as well as non-ferrous, which is to say it is non-ferrous. It doesn’t rust.
Copper crushes easily when compressed, and can create a good seal against liquids as well as pressure. And this is where it proves to be invaluable when involved with engineering practices.
The copper washer I removed from my injector, as well as those from others, was made from solid copper. There were no additives or inter-plated levels. In other words, as said… solid copper plate.
Now follows my past experience as well as in-depth scientific knowledge.
I used to own and rebuild BSA motorcycles. I did it on an annual basis, even if the machine was running perfectly. That is how I am! I need my machines to be perfect. Or… they might fail. I do not like failure!!!! I like my machines to work.
The copper washers used in my FL1’s Injectors were solid copper, as previously explained, and were pliable – if treated accordingly. My 1967 BSA A65-Thunderbolt motorcycle used solid copper head gaskets, which were expensive to replace; and as I did engine rebuilds annually this was an expensive outlay. I had a box of used gaskets in my garage, and felt there must be something I could do with them.
I used my in-depth knowledge of chemistry & physics to determine the gaskets could be renewed with a little bit of applied work & attention. And this is what I did –eventually.
I used a hand-held butane gas-burner to heat the gaskets to a level where they glowed red-hot. This burned off any impurities, etc, leaving the copper clean - although tarnished to the colour of a light-bronze.
The copper was allowed to cool at room temperature, which left it soft and once again… malleable.
I treated my injector’s washer in exactly the same way, which made it useable once more, except for the fact that some black carbon remained indented onto the surfaces.
Having blasted the copper-washer with intense heat, and allowed it to cool – slowly, I used a No2 file to gently clean the two flat surfaces back to polished copper. See the photo’s.
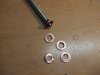
The file’s surface was perfectly flat so no undulations were left.
I reused the washer, and will do the rest the same way, when I work on my other Injectors - should I need to.
The method of heating and allowing the copper to cure is called, annealing. It is a method of softening metal from a super-heated level. It allows us the use of something we may have considered scrap. It enabled me to reuse something that seemed fit for scrap and not much more.
I now have a bag of spare washers.
And I know they are not expensive to buy but when faced with removing and refitting my No4 Injector with no spare copper-washer, I did as I have written and it works.
So there you have it. Recycling at its most basic level. Injector level.
And before anyone suggests otherwise, my injector is gas/oil/compression tight & sealed. It really does work. Jeez, I'm a scientist & my work has to be perfect! Don't ask questions, though.
Copper is not that much different to other metals. It is malleable as well as non-ferrous, which is to say it is non-ferrous. It doesn’t rust.
Copper crushes easily when compressed, and can create a good seal against liquids as well as pressure. And this is where it proves to be invaluable when involved with engineering practices.
The copper washer I removed from my injector, as well as those from others, was made from solid copper. There were no additives or inter-plated levels. In other words, as said… solid copper plate.
Now follows my past experience as well as in-depth scientific knowledge.
I used to own and rebuild BSA motorcycles. I did it on an annual basis, even if the machine was running perfectly. That is how I am! I need my machines to be perfect. Or… they might fail. I do not like failure!!!! I like my machines to work.
The copper washers used in my FL1’s Injectors were solid copper, as previously explained, and were pliable – if treated accordingly. My 1967 BSA A65-Thunderbolt motorcycle used solid copper head gaskets, which were expensive to replace; and as I did engine rebuilds annually this was an expensive outlay. I had a box of used gaskets in my garage, and felt there must be something I could do with them.
I used my in-depth knowledge of chemistry & physics to determine the gaskets could be renewed with a little bit of applied work & attention. And this is what I did –eventually.
I used a hand-held butane gas-burner to heat the gaskets to a level where they glowed red-hot. This burned off any impurities, etc, leaving the copper clean - although tarnished to the colour of a light-bronze.
The copper was allowed to cool at room temperature, which left it soft and once again… malleable.
I treated my injector’s washer in exactly the same way, which made it useable once more, except for the fact that some black carbon remained indented onto the surfaces.
Having blasted the copper-washer with intense heat, and allowed it to cool – slowly, I used a No2 file to gently clean the two flat surfaces back to polished copper. See the photo’s.
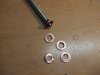
The file’s surface was perfectly flat so no undulations were left.
I reused the washer, and will do the rest the same way, when I work on my other Injectors - should I need to.
The method of heating and allowing the copper to cure is called, annealing. It is a method of softening metal from a super-heated level. It allows us the use of something we may have considered scrap. It enabled me to reuse something that seemed fit for scrap and not much more.
I now have a bag of spare washers.
And I know they are not expensive to buy but when faced with removing and refitting my No4 Injector with no spare copper-washer, I did as I have written and it works.
So there you have it. Recycling at its most basic level. Injector level.
And before anyone suggests otherwise, my injector is gas/oil/compression tight & sealed. It really does work. Jeez, I'm a scientist & my work has to be perfect! Don't ask questions, though.
Last edited: