I got a new set of bolts for the front cover, and got that fitted, i also rebuilt the selectors. sadly i found that one of the retaining bolts on the selectors was worn through and wasn't holding the fork in place. also did not have another bolt to replace it. So this job is still ongoing.
all sealed in.
Fairey Ovderdrive
As the gearbox is on the bench i've started work on stripping the overdrive down.
this guide has been the most useful thing i could use
http://www.lrsoc.com/forum/forum_files/Overdrive Repair and Service Manual.pdf
it has really clear instructions, step by step with photos on how to dissemble and rebuild the box.
also has standard part numbers for lots of the bearings.
I got this about 2 years ago, i was assured it had just been removed and was in perfect order. I honestly didn't even know how to check at the time.
It's been sat in a corner of the garage since then.
When i picked it up a few weeks ago, it was completely solid. no moving parts. not a good sign.
I've stripped it down, and unsurprisingly it's not in the best shape inside.
On the bench
Started by removing the rear plate, and then working through the circlips that retain everything onto the mainshaft
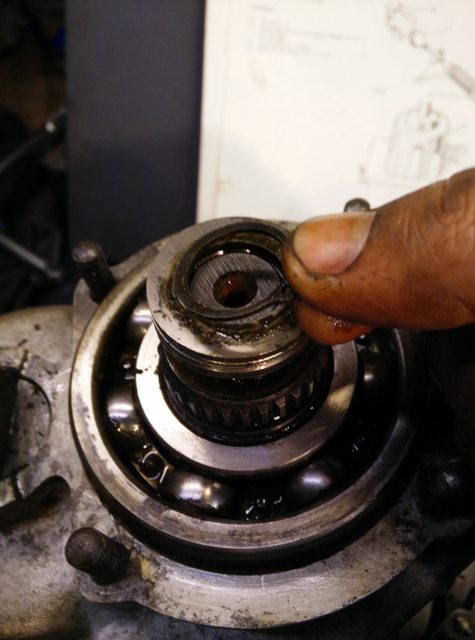
the first thrustwasher was a bit grim, but wasn't really in bad nick after a clean
there are various shims and thrust bearing races along the way, it makes sense to keep everything together even if you are replacing them anyway.
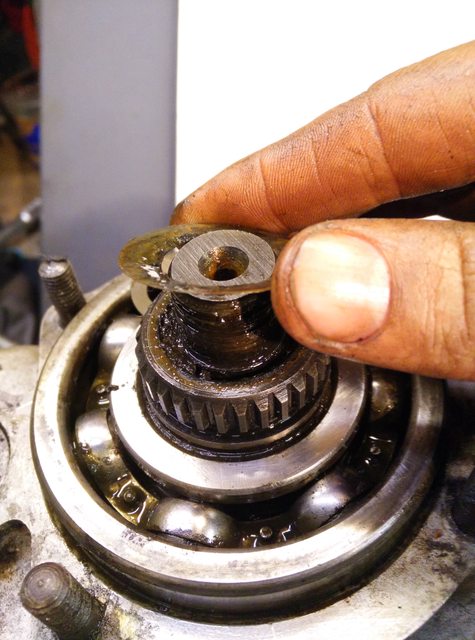
this distance piece was one of the first signs of what the inside might be like
I then removed the bolt holding the selector fork
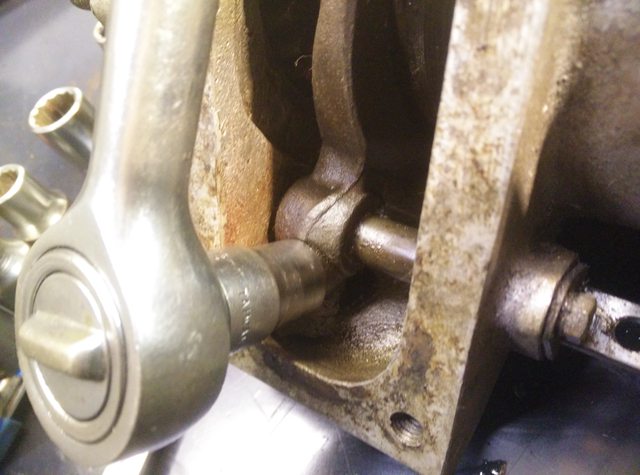
i then took the grub screws out and removed the shaft.
annoyingly i missed the second screw because of grime and not reading instructions properly. i figured it was all seized until i found the second grub screw, then the whole shaft slid straight out.
next, i found the assembly with the main bearing and the rear gear, would not come away from the shaft, i only have one suitable puller, it was a bit fiddle but i managed to get it pulled away
the first of the roller bearings came out, filthy and rusty and horrible
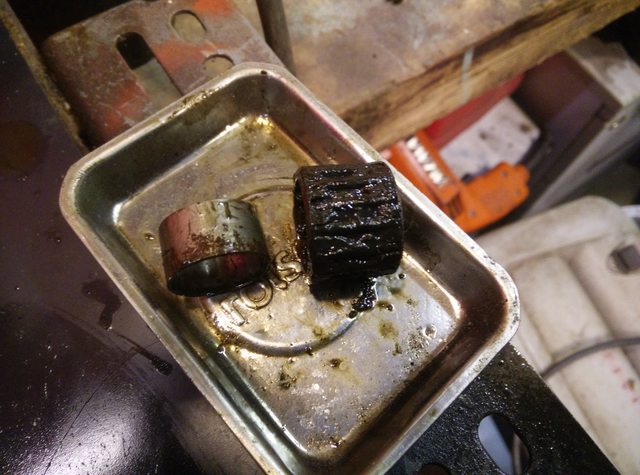
I've tried to keep everything in bags or taped together so i have an idea of what's what.
there's a surprising amount of parts in here, and weirdly it seems like a much better bit of engineering than the actual gearbox
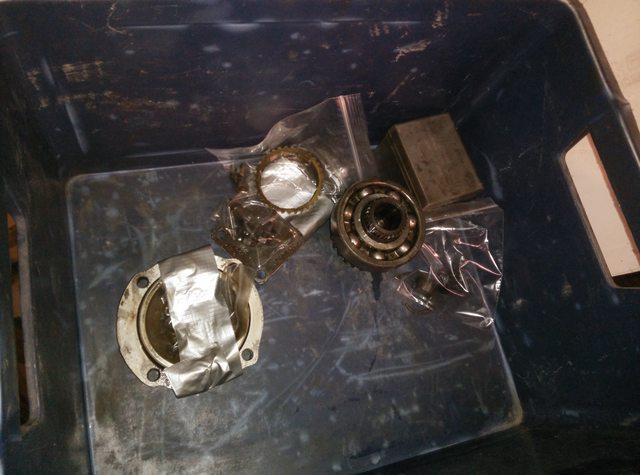
magnetic dishes are a massive help with this job
the synchro centre part. everyone warns you about the springs flying out and losing the ball bearings. its true. fortunately i found them easily
After disassembly, the centre shaft drops straight out
the description i read, said to just withdraw the layshaft so it could be disasembled.
it would not move. it wasn't turning freely inside the gear either.
I ended up having to hold the main gear to steady it, and had to whack the edge of the layshaft end with a copper mallet, so that it would release from the laygear
i was then able to completely remove the layshaft easily
i then tapped the bearing and seals out of the casing
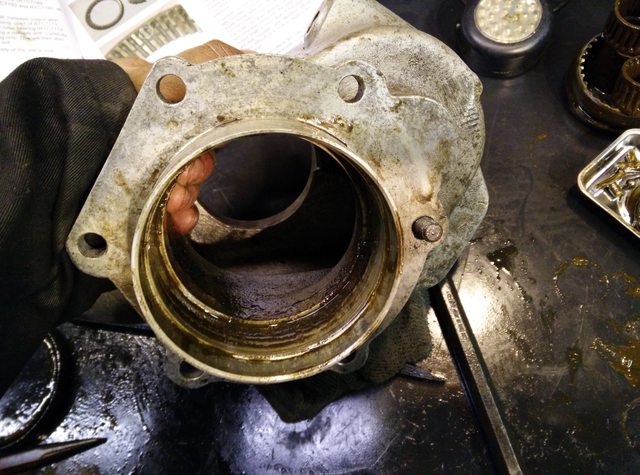
the bearing may have been reusable, but it got damaged as i didn't have a suitible drift. the casing has no damage though
some of the other bearings look much better than the first, but i will still try to replace. although these are not cheap
Currently i cannot separate these, i don't want to try to be too forceful with the puller as i dont want to damage anything
that's where i'm at currently, i have taken the parts list to a local bearing shop, and they have given me a fairly reasonable price list. i'm just going to shop around and make sure its the bes ti can get.
next step is rebuild it and fit