BULKHEAD REPAIRS (partial) DAY TWO continued
End cap on the side of the dashboard - passenger side - left hand side needs to be replaced. I haven't found someone who makes it so I guess I need to give it a bash me self (pun intended)
#####
Additional information #1
The basic method I'm using is using "Hammer forms". Essentially these are solid shapes onto which you form sheet metal. It isn't rocket science: Make the shape you want and "drape" the sheet metal over it (it is as simple as that).
I'm using wood for the basic shape - but as you will see in a bit it isn't up to the job for the more complicated corners.
#####
Here's cutting out the simple shape.
This is a softwood plywood - not ideal - but it is available and free
The lump at the end of the door catch tube turned out to be a separate bit after all (compared both sides of the bulkhead)
(Bit of a tip for using an angle grinder on complicated shapes - hold it against your body in this downwards manner - but make sure workpiece doesn't move so you end up spinning the wheel into ya nuts)
Cutting out the rough shape =>
I know I'll probably sound like a real old fuss pot: But make sure you de-burr! Save your fingers! Metal sliver cuts are not nice.
Clamping the metal between two bits of wood is important. If you try to bend the sheet over the edge of the form without some clamping on the back the sheet will just bulge on both sides of the bend.
Straight bends work well with this soft plywood form...
Take your time and use a really light hammer to try and bend the sheet as close to the edge of the wood as possible. If you bash the furthest edge you will end up with ripples. Try and get the hammer head right into the edge between the two bits of wood.
Look it really is a light weight hammer =>
(When I grow up I'll be allowed to use the big hammer)
Curved edge - harder to achieve as you are stretching the metal round a shape instead of folding along a straight edge.
#####
Additional information #2
The next method I'm using in addition to using "Hammer forms" is a method called "flow forming"
See this =>
Or this =>
You can buy (rather expensive) tools for this if you want =>
https://www.tinmantech.com/products/hand-tools/flow-forming/
Now - me being me - I'm tempted to zoom off on another tangent and reproduce the posh tools above (and I still have plans for this) but I've decided to just use the new air riveting set I got from skinpins =>
#######
Air riveting kit came with a nicely polished elephant's foot...
...which if you want to keep nice it is worth covering with lumps of masking tape...
Starting to bend with the lightweight hammer - ideally you should stop before you start leaving marks in the surface (doh)!
Finish the shape with the air rivet gun
Wood started to crack and fall apart.
I now need to make a metal form for this bit (to be continued)
More edge trimming (this time with tin snips)
Whoops - over did that bit!
Hammer it flat again (on a vice anvil section)
Well - here's how far I got today. I've got the rough shape of the new panel.
Sorry I held it the wrong way round in this picture. Metal (anvil) like hammer forms will be made to help finish off the complicated shapes.
To be continued.
End cap on the side of the dashboard - passenger side - left hand side needs to be replaced. I haven't found someone who makes it so I guess I need to give it a bash me self (pun intended)
#####
Additional information #1
The basic method I'm using is using "Hammer forms". Essentially these are solid shapes onto which you form sheet metal. It isn't rocket science: Make the shape you want and "drape" the sheet metal over it (it is as simple as that).
I'm using wood for the basic shape - but as you will see in a bit it isn't up to the job for the more complicated corners.
#####
Here's cutting out the simple shape.
This is a softwood plywood - not ideal - but it is available and free
The lump at the end of the door catch tube turned out to be a separate bit after all (compared both sides of the bulkhead)
(Bit of a tip for using an angle grinder on complicated shapes - hold it against your body in this downwards manner - but make sure workpiece doesn't move so you end up spinning the wheel into ya nuts)
Cutting out the rough shape =>
I know I'll probably sound like a real old fuss pot: But make sure you de-burr! Save your fingers! Metal sliver cuts are not nice.
Clamping the metal between two bits of wood is important. If you try to bend the sheet over the edge of the form without some clamping on the back the sheet will just bulge on both sides of the bend.
Straight bends work well with this soft plywood form...
Take your time and use a really light hammer to try and bend the sheet as close to the edge of the wood as possible. If you bash the furthest edge you will end up with ripples. Try and get the hammer head right into the edge between the two bits of wood.
Look it really is a light weight hammer =>
(When I grow up I'll be allowed to use the big hammer)
Curved edge - harder to achieve as you are stretching the metal round a shape instead of folding along a straight edge.
#####
Additional information #2
The next method I'm using in addition to using "Hammer forms" is a method called "flow forming"
See this =>
Or this =>
You can buy (rather expensive) tools for this if you want =>
https://www.tinmantech.com/products/hand-tools/flow-forming/
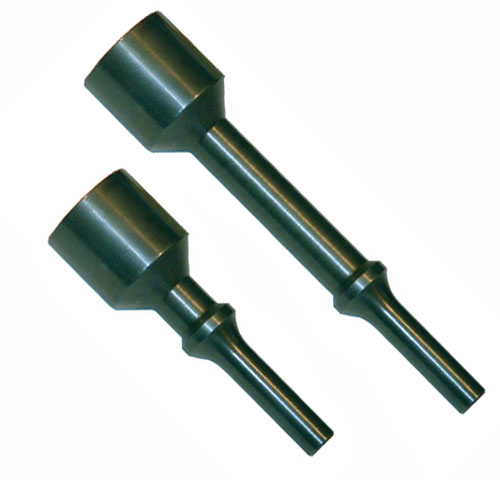
Now - me being me - I'm tempted to zoom off on another tangent and reproduce the posh tools above (and I still have plans for this) but I've decided to just use the new air riveting set I got from skinpins =>
#######
Air riveting kit came with a nicely polished elephant's foot...
...which if you want to keep nice it is worth covering with lumps of masking tape...
Starting to bend with the lightweight hammer - ideally you should stop before you start leaving marks in the surface (doh)!
Finish the shape with the air rivet gun
Wood started to crack and fall apart.
I now need to make a metal form for this bit (to be continued)
More edge trimming (this time with tin snips)
Whoops - over did that bit!
Hammer it flat again (on a vice anvil section)
Well - here's how far I got today. I've got the rough shape of the new panel.
Sorry I held it the wrong way round in this picture. Metal (anvil) like hammer forms will be made to help finish off the complicated shapes.
To be continued.
Last edited: