Another thought Rob - ALooy wheel repairers
Thanks Joe - the mode of crack in is as you describe, except I was using a torque wrench with just 15Nm dialled in. No over torqued, but presumably already cracked.
I'll try the braze with the stuff Alibro found: it seems an interesting product, plus, as you say, it isn't exactly a critical screw.
I'll attemp to drill stop - but access to the larger crack is extremely limited.
We shall see...
Hi Rob,
It may well be ok with the soft braze stuff - I have used Durafix before (identical to the stuff in the video - they are all the same imo

) - and it was 'ok' it all depends on what you can get to. I have used it on a marine diesel heat salt water / fresh water exchanger. It seems quite impressive but be prepared to use quite a few rods getting the temps and condition correct. Also the cleanliness is vital. Use acetone and allow to dry or flash off with the torch (watch the eyebrows lol)
The only problem was - that I was not 100% convinced and if it had have been my heat exchanger I would have had it welded. (Just a mind f^ck thing really...

- it was probably great - but ..... and it was rather important as water INSIDE a Yacht is NOT a good thing...

)
The owner of the boat also decided to get it welded when he had access to an alloy casting fab / tig guy.
On yours, I think the difficulty is going to be in the areas I have marked on the image of yours (a part of re-posted here).
This area will be a fairly deep internal crack in the casting that you are unlikely to get the stuff into. TIG can easily get in there and at least bond the outside of the casting for perhaps 5 mm or so with a small groove whizzed out with the carbide / diamond cutter or similar in a die grinder.
It is the one sort of job that I think will be difficult for the Durafix to do it's stuff as the Durafix really needs surface area you can get to to effectively coat (a bit like solder tinning action) before any joining action or coating action. - but - again - maybe it will be ok and flow into the joints .. not something I had much success with but I was running out of rods as getting the heat right was a pain.... The other BIG issue may be actually getting heat into the area !!. (
note all the 'demos' are on easily heated small pieces.). your cylinder head will act like a HUGE heat sink and getting the temp of the existing casting up will be extremely difficult - to say the least - also the trouble is if you open out the marked areas (which I believe need doing - then the casting piece may well fall off.

. - Then it really is TIG. It is just a bit of a bu&&er to get to (from what I can see)
TIG can also provide an instant heat weld without the heat sinking issues of a low melt product.
here is the image of where (from what I can see and judge) I am sure it is quite cracked underneath and will only be held by a small surface area as the cracked 'chuck bent outward farther at the top - splitting the top / sides but would have cracked inside at the bottom area and bent slightly.
See how you go on. It will be really interesting how the stuff performs. I bet that heat exchanger is probably still going

I am not being negative - sorry if it seems that way - just looking at it from what I would do - however - I worry if there is a slight bit of oil on my engine

- others never look under the bonnet and even if they do, some like the cruddy oil and diesel coating of some units as it "stops rusting and parts seizing"




- or as an old guy said to me when we were live aboard sailing - (ref his old perkins 4107) 'If it aint got oil all over it there's summat wrong'...
He always said my Mercedes OM636 was far too clean - "must be summat up wi' it"...... (I kept the Merc' green paint hidden)
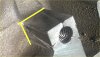