Finished work at about lunchtime and discovered that the LR Direct order had arrived:
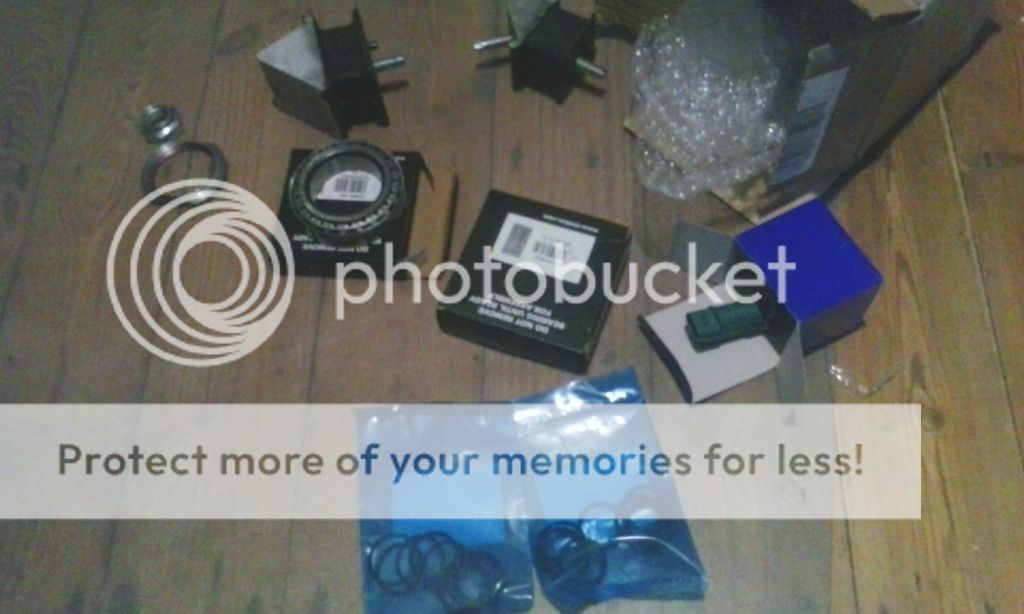
So I got busy. Bearing tapped onto what will be the rear end of the mechanism.
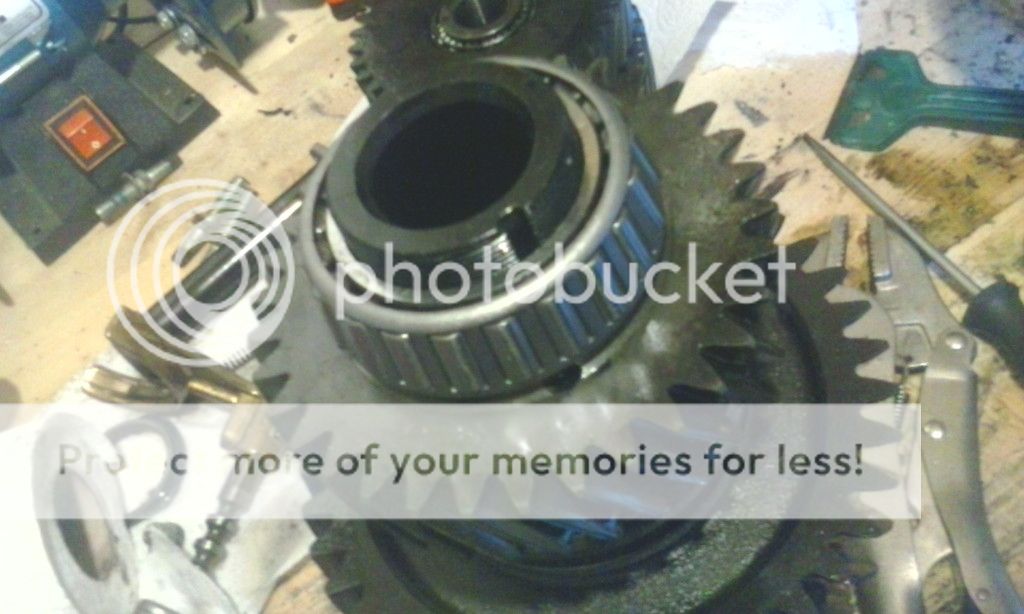
There's a nut that goes on that threaded part, but I don't think I took a picture of that. Next is the problem of getting the outer bearing shell out of the front nose cone. There isn't much room to get a drift in:
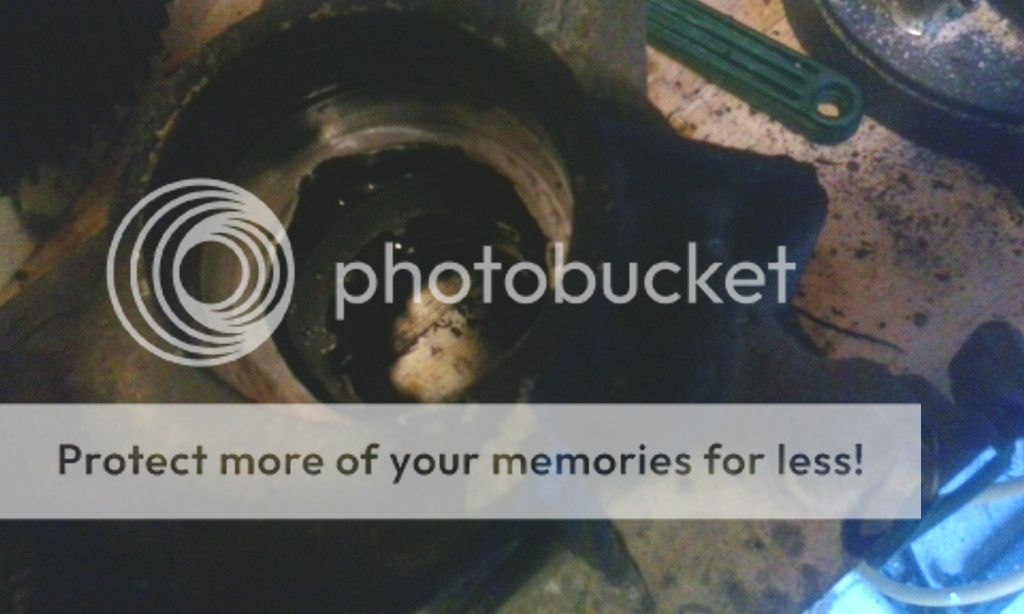
A screwdriver shank just squeezed past the difflock selector mechanism, so it came out. That hole in the middle looks a bit jagged. Not my fault, honest. It just seems to be an unfinished casting edge. Anyway, all the critical surfaces are OK, so let's tap an outer bearing shell into the recess:
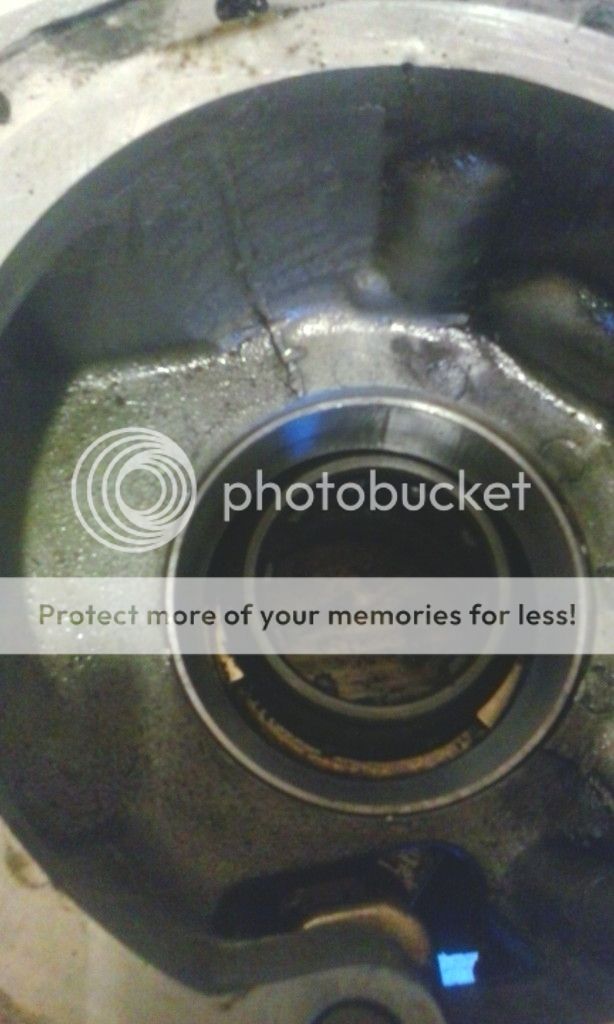
Now let's put that plate on the side that covers the difflock selector mechanism:
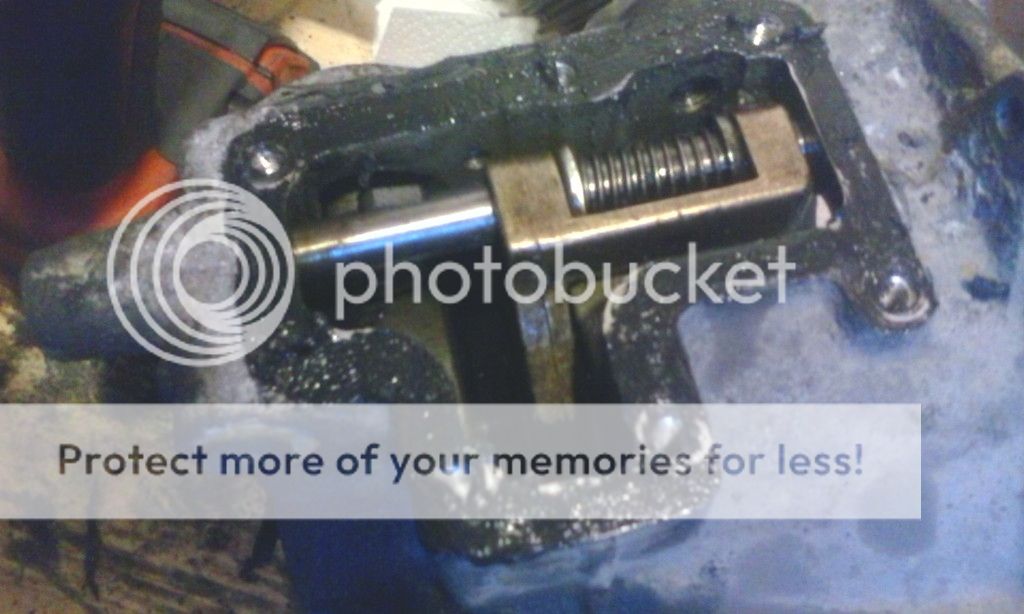
Lots of instant gasket going into this build, because there didn't seem to be any paper ones fitted and there was only sealant where components were joined together. In order to provide a seat for the rear bearing the rear nose come containing the speedo drive has to go on. A bit of sealant:
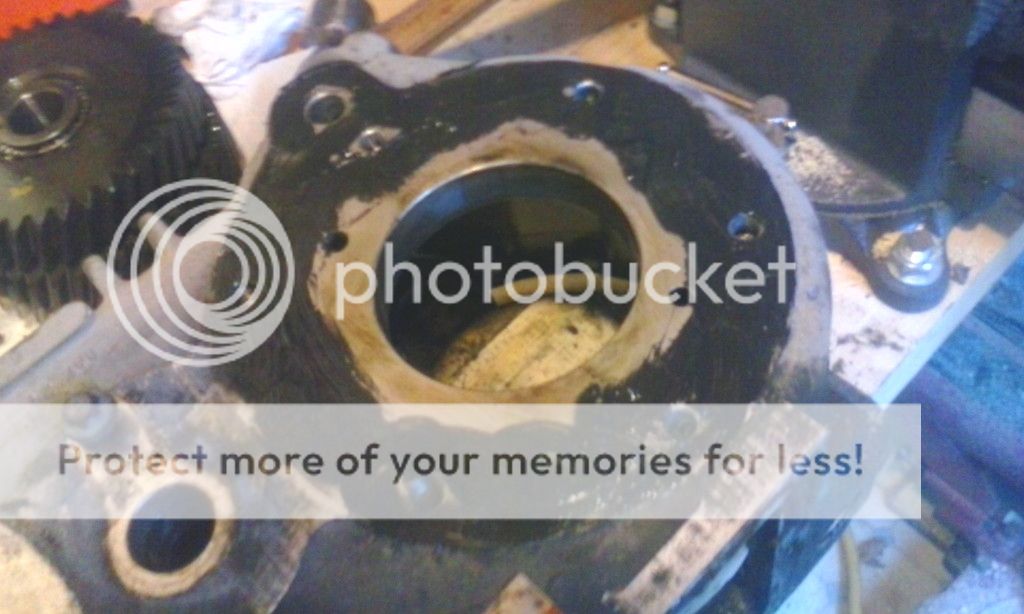
And on it goes:
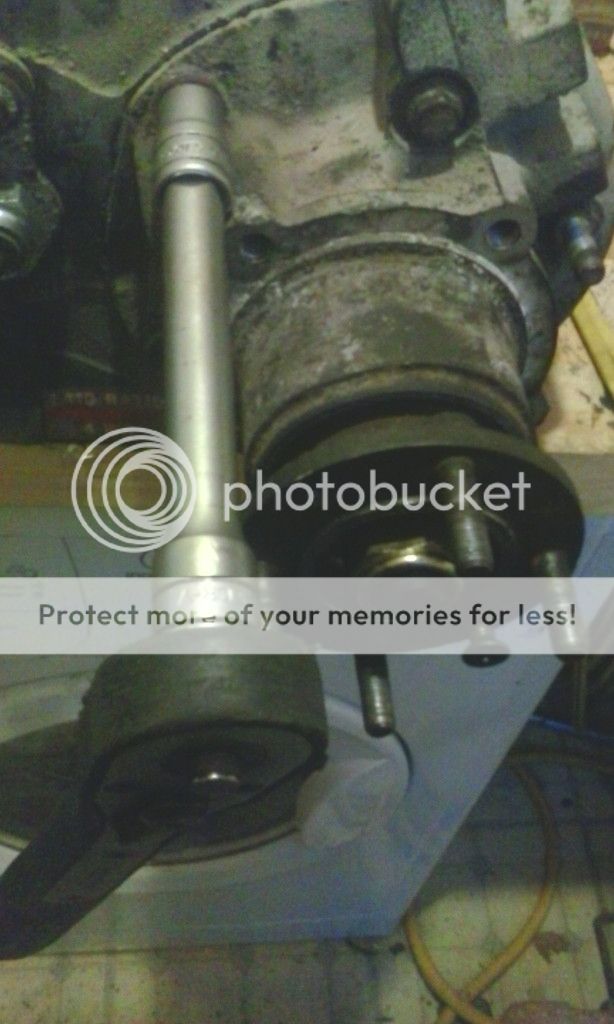
Then we'll offer the mechanism up to see if it all fits:
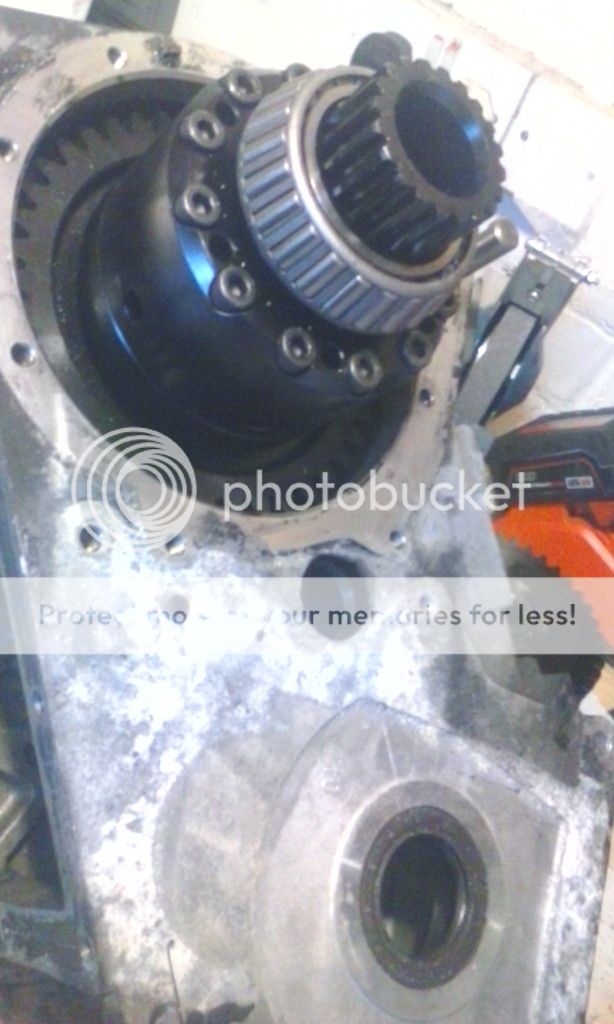
Yup, that's gone in nicely. So I put the front nose cone on. The mechanism turned stiffly but smoothly, so I think we can count that as a success. Now let's see if it will change gear. Oh no, the fork isn't in the correct groove in the splined slider:
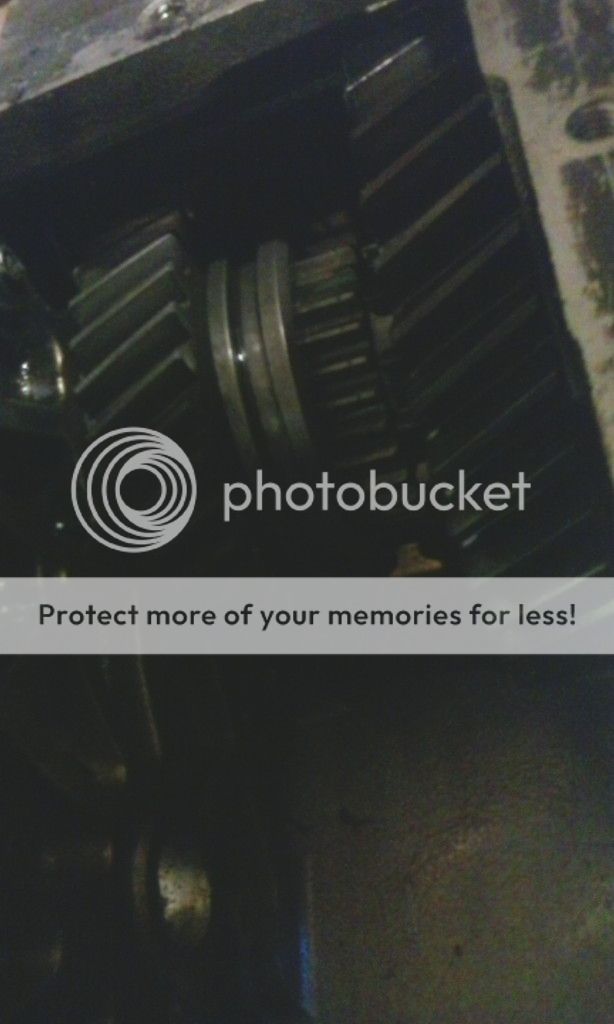
So it's got to come apart again. I could have sworn it was in the right place when I put the mechanism in the casing. Right, now that's a bit better. Next let's get the intermediate gears in. Here's the centre shaft just about to have an O ring put in its groove before being tapped home:

Now let's get a fresh bearing on the output shaft:
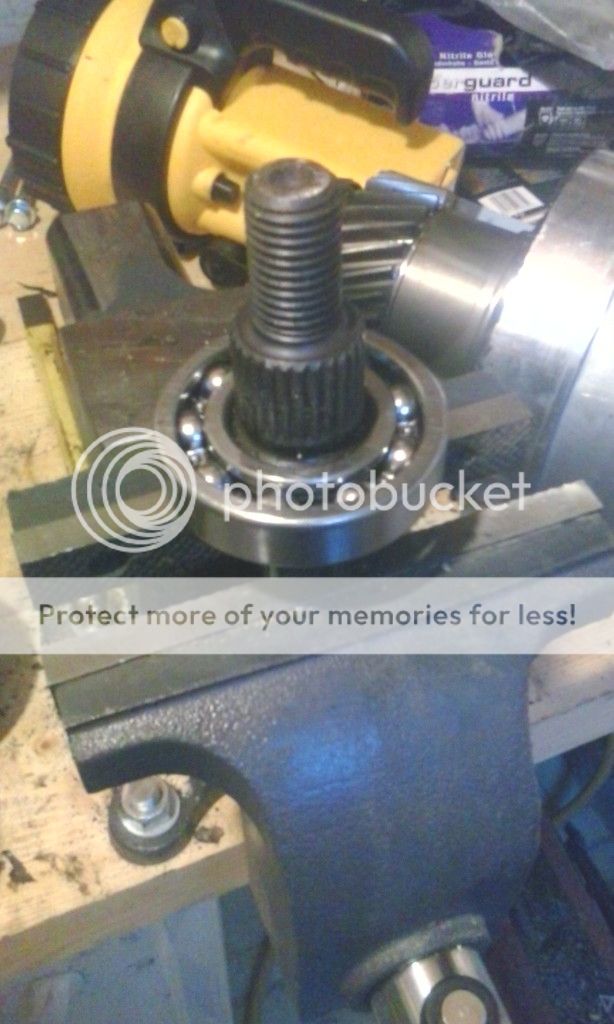
And there's the front flange and shaft back in position:
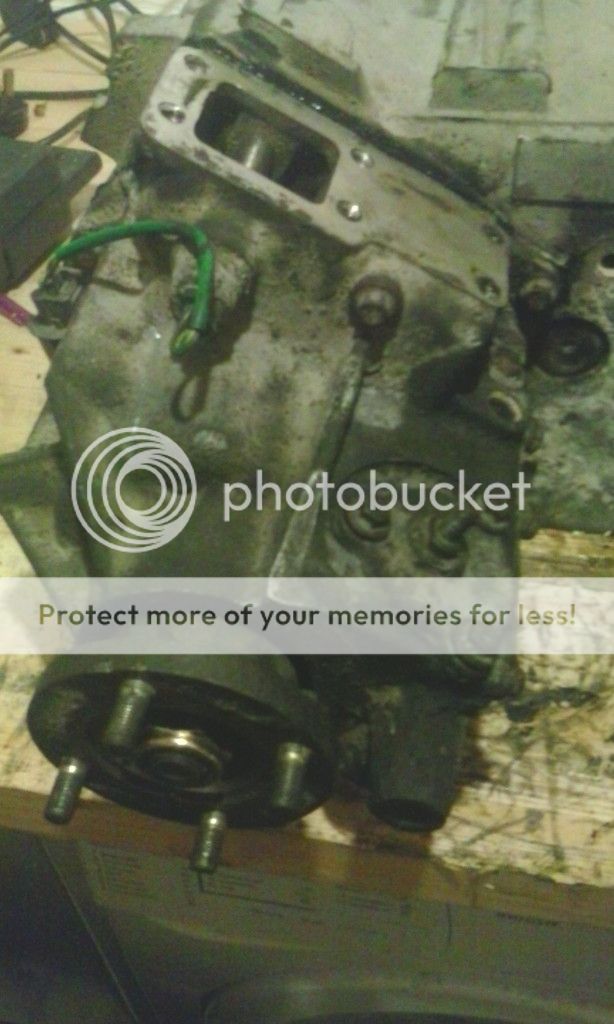
Then I remembered I'd forgotten to knock in the flange on the nut that holds the bearing to the shaft of the diff. Everything was pretty tight, so it's hard to imagine it going anywhere, but for peace of mind I spun the bolts out of the rear nose cone and staked it in, and then put the rear cone back on:
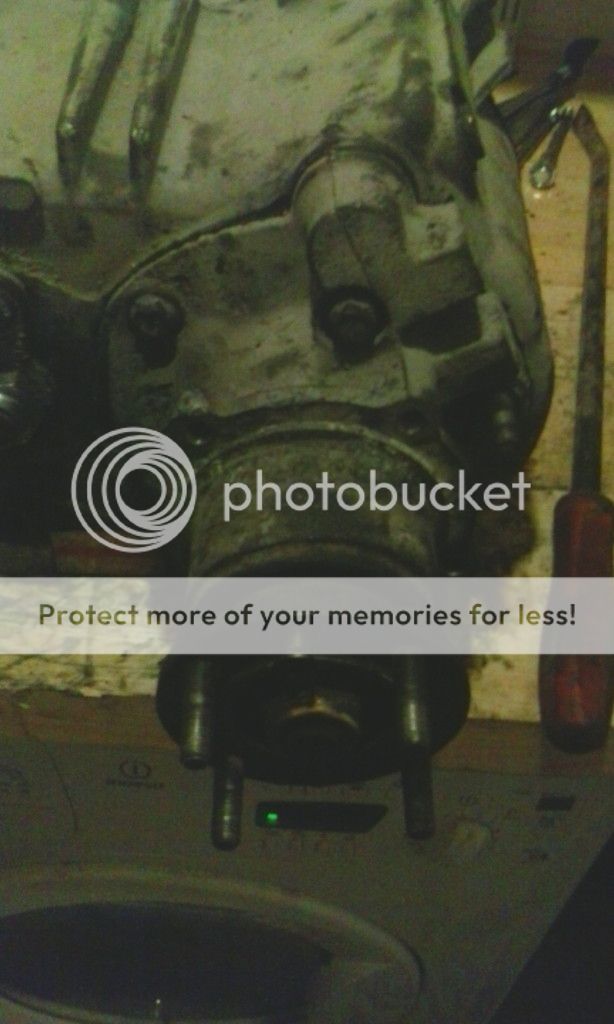
Feels like a good afternoon's work. If it wasn't for the couple of mistakes where I had to do some dismantling it would have been even quicker. It's quite a clever design. The final drive mainshaft is in fact the diff body.
It's great when you flick the lever on the ratchet from anticlockwise to clockwise. Or these days, push the switch on the impact gun. The box is a little stiffer to turn than it was before, but I'm pretty confident in the bearings. There's a tiny bit of rotational slack, but that's just the splines. I didn't take it out and offer it up to the car, because I was losing the light. But maybe I'll give it a go tomorrow.