Today, I removed the Fuel-rail pressure sensor, the one that has been problematic for a while.
Having fabricated a replacement cable with a new plug, using an in-line 3-pin connector that enabled me to change cables/connecting-plugs with ease, both the original plug as well as the new replacement failed. That persuaded me to carry out some checks on the sensor itself.
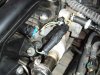
My plan was to tin the sensor’s three connectors with solder, but only after an in-depth inspection.
I discovered the connectors were made of brass, which was both expected and hoped for.
The brass, however, was heavily tarnished, where electrical continuity could easily have broken down – and probably did! It’s a common fallacy that copper & brass do not corrode. They do, but not like steel or iron. The copper in the brass alloy tarnishes as it attempts to return to its original ore, malachite. This is green in colour, by the way.
I cleaned the connectors with carb-cleaner followed by a contact-cleaner spray. The socket and the connectors were immaculate. I saw the tarnishing after the cleaning, using a x10 hand-lens. I suppose I could have given them a bit of a rub down, using a nail-file/board borrowed from my wife. However, the fault would soon return, I’m sure.
I tinned the connectors, using my trusty soldering-iron. The solder contained flux for a clean & tidy operation.
If you try this yourself, you must first ensure the connectors are scrupulously clean. Preparation is all important.
With the soldering done and the sensor refitted - with the plug reconnected, the engine started easily. A run proved all was well.
I’ve actually bought a new replacement sensor, Part No: LR009732 and if it goes well with my tinning method it will be carried as a spare in my pack-up, along with the ½” drive socket, etc, for removing it.
There is one thing more, and it’s puzzling. There was no seal fitted with the sensor. There should have been an appropriate seal (a copper crush-washer) and its absence makes me believe I’m not the first to remove this sensor. I fitted an appropriate washer from my stock of parts – see the photo, and tested the system for leaks and functionality. All is good.
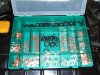
I will now be monitoring how the fuel system operates with my soldering repair. I’m expecting it to be as good as new. Fingers crossed.
Having fabricated a replacement cable with a new plug, using an in-line 3-pin connector that enabled me to change cables/connecting-plugs with ease, both the original plug as well as the new replacement failed. That persuaded me to carry out some checks on the sensor itself.
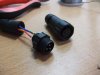
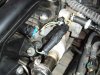
My plan was to tin the sensor’s three connectors with solder, but only after an in-depth inspection.
I discovered the connectors were made of brass, which was both expected and hoped for.
The brass, however, was heavily tarnished, where electrical continuity could easily have broken down – and probably did! It’s a common fallacy that copper & brass do not corrode. They do, but not like steel or iron. The copper in the brass alloy tarnishes as it attempts to return to its original ore, malachite. This is green in colour, by the way.
I cleaned the connectors with carb-cleaner followed by a contact-cleaner spray. The socket and the connectors were immaculate. I saw the tarnishing after the cleaning, using a x10 hand-lens. I suppose I could have given them a bit of a rub down, using a nail-file/board borrowed from my wife. However, the fault would soon return, I’m sure.
I tinned the connectors, using my trusty soldering-iron. The solder contained flux for a clean & tidy operation.
If you try this yourself, you must first ensure the connectors are scrupulously clean. Preparation is all important.
With the soldering done and the sensor refitted - with the plug reconnected, the engine started easily. A run proved all was well.
I’ve actually bought a new replacement sensor, Part No: LR009732 and if it goes well with my tinning method it will be carried as a spare in my pack-up, along with the ½” drive socket, etc, for removing it.
There is one thing more, and it’s puzzling. There was no seal fitted with the sensor. There should have been an appropriate seal (a copper crush-washer) and its absence makes me believe I’m not the first to remove this sensor. I fitted an appropriate washer from my stock of parts – see the photo, and tested the system for leaks and functionality. All is good.
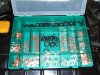
I will now be monitoring how the fuel system operates with my soldering repair. I’m expecting it to be as good as new. Fingers crossed.