dirtyrhino
New Member
- Posts
- 617
Looks like that's plated behind the hanger-oddly only partially along the leg though 
That'll need cleaning up and plating properly, and where the rots set in, that'll need chopping out, treating and plating to make it all nice and solid. last thing ya want is for the hanger to collapse on you mid-journey. From the pics, that plate looks OK, and so does the weld...I think. tell me to bugger off, but if yer keen on doing it, i'd suggest spending some time on some chassis plating......
If this overlap goes the whole length of that plate - your onto a winner, as it's make a great butt for welding a decent side plate onto it cos it'll help fight gravity
Also, see that plate alongside the gaping hole....that'll help with a bottom plate aswell.
Chop out the ****e, get it treated, and then get some 4mm plate cut to shape and have some fun with yer Mig
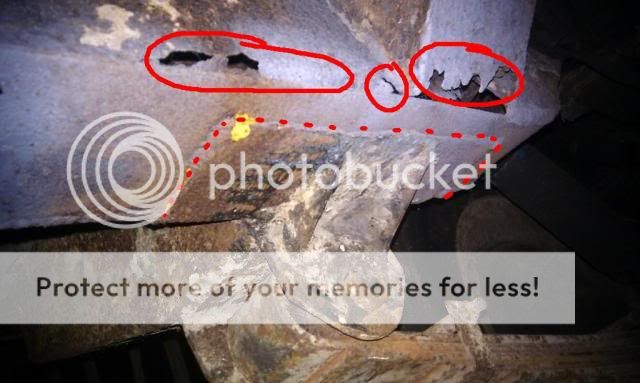
That'll need cleaning up and plating properly, and where the rots set in, that'll need chopping out, treating and plating to make it all nice and solid. last thing ya want is for the hanger to collapse on you mid-journey. From the pics, that plate looks OK, and so does the weld...I think. tell me to bugger off, but if yer keen on doing it, i'd suggest spending some time on some chassis plating......
If this overlap goes the whole length of that plate - your onto a winner, as it's make a great butt for welding a decent side plate onto it cos it'll help fight gravity
Also, see that plate alongside the gaping hole....that'll help with a bottom plate aswell.
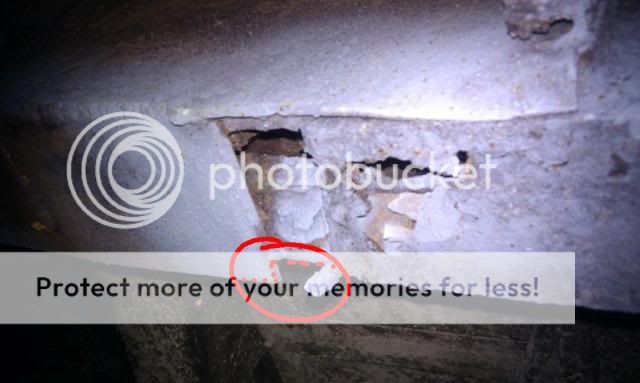
Chop out the ****e, get it treated, and then get some 4mm plate cut to shape and have some fun with yer Mig
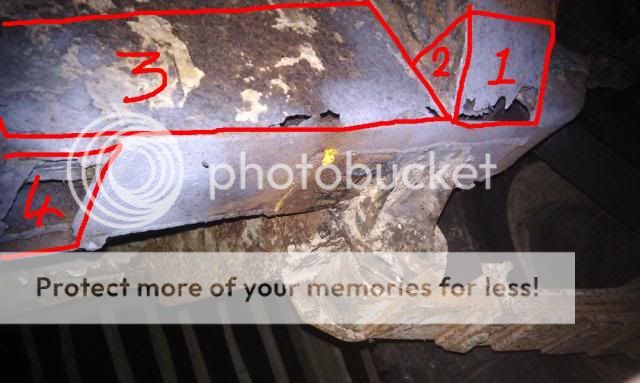