owl
Well-Known Member
- Posts
- 1,807
- Location
- Breaston Derbyshire
The drawings in the workshop manuals are not to scale, they are ok for the position of outriggers and mounting brackets etc but not the shape of the main chassis rails.
If you have an old chassis you can use that to make templates and a jig to build your new one in. I made this template of a 109 chassis.
then used the template to make a jig.
If you have an old chassis you can use that to make templates and a jig to build your new one in. I made this template of a 109 chassis.
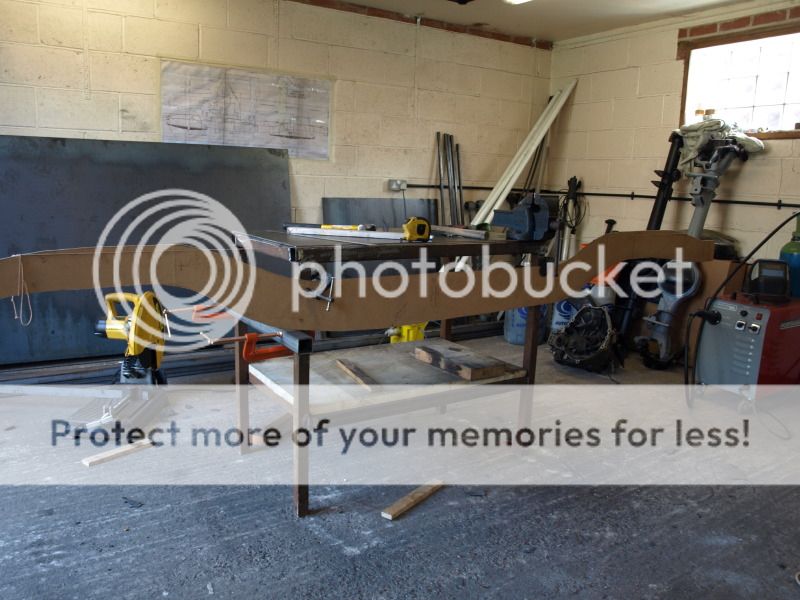
then used the template to make a jig.
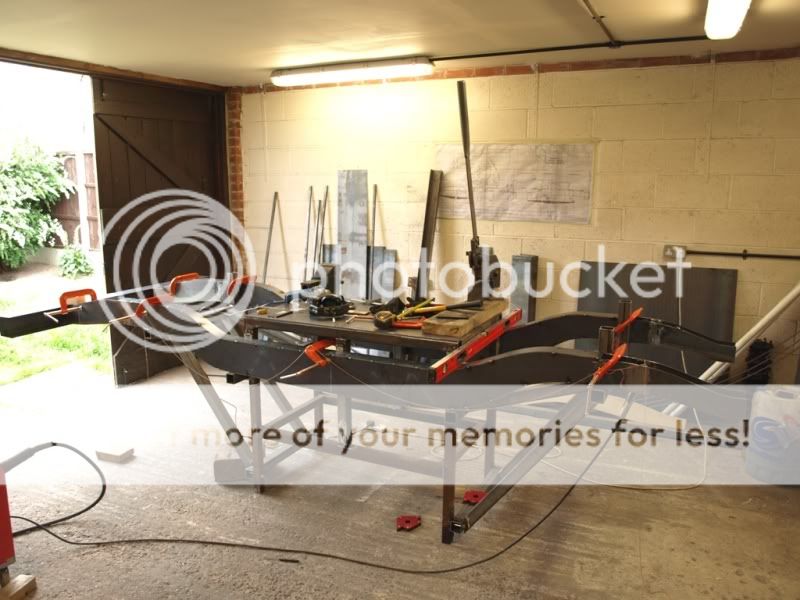