Evening all,
Backstory: My Granddad has had this 109" diesel since the mid-eighties, before that his Dad maintained it from new when he worked as a mechanic at Co-Op. The Series 3 was their recovery vehicle, fitted with a lift and tow crane in the rear tub.
Ever since I remember, I would wander around my Granddads old workshop in awe of this great Land Rover, constantly asking if I could have it. My wish was granted on my 16th birthday when it was handed over officially, although it took another 11 years for me to make a start on doing anything to it.
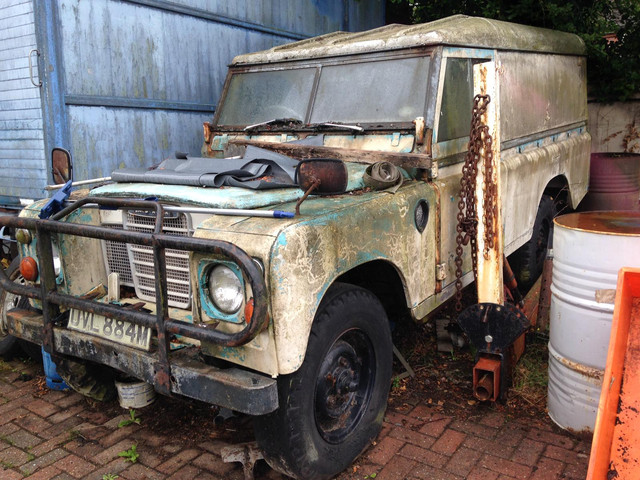
Starting Point: As you can see from the photos, it was in a pretty dire state. Chassis completely rotten, bulkhead beyond salvage and only really held together by some of the body panels. Knowing it would need at least a new chassis and bulkhead is why I took so long to get started; lack of time, money and motivation. It took a friend at work to start on his 88" 1973 diesel to really get me started, sharing some motivation and ideas together.
The Plan: I knew it would have to be built up on a replacement chassis, so it might as well be galvanised. My initial thoughts were to do a full rebuild, but with limitations. So I didn't want to strip major components unless they needed it, but everything that could be easily replaced would be. Time will tell how well that plan holds up, I'm well aware this will always be an on-going project, but I also want to make sure it's well finished and not just bodged together.
I'm fortunate enough to have a full workshop at work (mechanic by trade), along with access to a full metal-smith shop. However I'm not able to do the full build there; my plan is to strip the whole vehicle where it is at my Granddads yard, then bring components to work to rebuild, swapping them out along the way, hopefully onto a galvanised chassis.
Backstory: My Granddad has had this 109" diesel since the mid-eighties, before that his Dad maintained it from new when he worked as a mechanic at Co-Op. The Series 3 was their recovery vehicle, fitted with a lift and tow crane in the rear tub.
Ever since I remember, I would wander around my Granddads old workshop in awe of this great Land Rover, constantly asking if I could have it. My wish was granted on my 16th birthday when it was handed over officially, although it took another 11 years for me to make a start on doing anything to it.
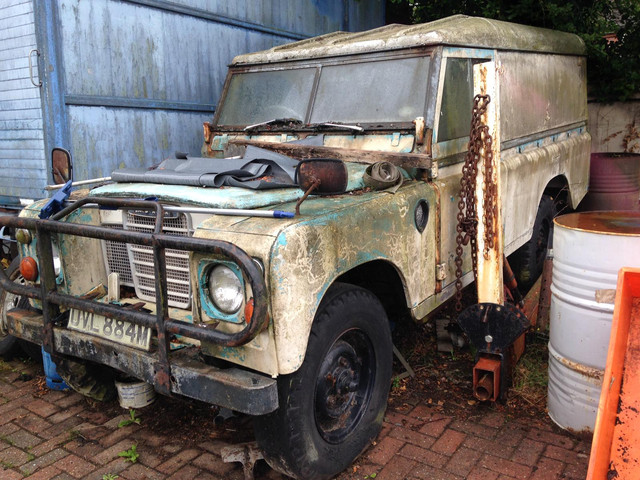
Starting Point: As you can see from the photos, it was in a pretty dire state. Chassis completely rotten, bulkhead beyond salvage and only really held together by some of the body panels. Knowing it would need at least a new chassis and bulkhead is why I took so long to get started; lack of time, money and motivation. It took a friend at work to start on his 88" 1973 diesel to really get me started, sharing some motivation and ideas together.
The Plan: I knew it would have to be built up on a replacement chassis, so it might as well be galvanised. My initial thoughts were to do a full rebuild, but with limitations. So I didn't want to strip major components unless they needed it, but everything that could be easily replaced would be. Time will tell how well that plan holds up, I'm well aware this will always be an on-going project, but I also want to make sure it's well finished and not just bodged together.
I'm fortunate enough to have a full workshop at work (mechanic by trade), along with access to a full metal-smith shop. However I'm not able to do the full build there; my plan is to strip the whole vehicle where it is at my Granddads yard, then bring components to work to rebuild, swapping them out along the way, hopefully onto a galvanised chassis.
Last edited: